Your Trusted Expert in Motion and Attitude Control Solutions
We provide high-precision accelerometers, gyroscopes, and inertial navigation systems (INS) for reliable motion and attitude control. Trust our expertise to deliver tailored solutions for aerospace, automotive, marine, and industrial applications.
What Problems We Can Solve
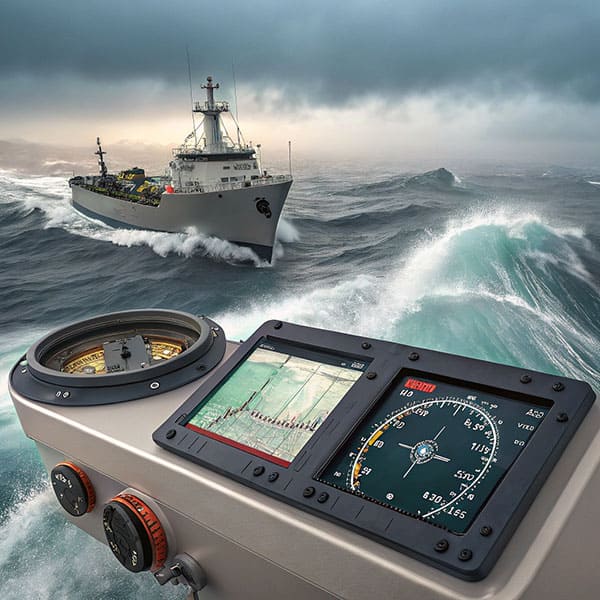
Accurate Motion Detection
Gyroscopes and accelerometers provide highly accurate motion sensing, offering reliable measurements of angular velocity, acceleration, and position in real-time, regardless of external disturbances
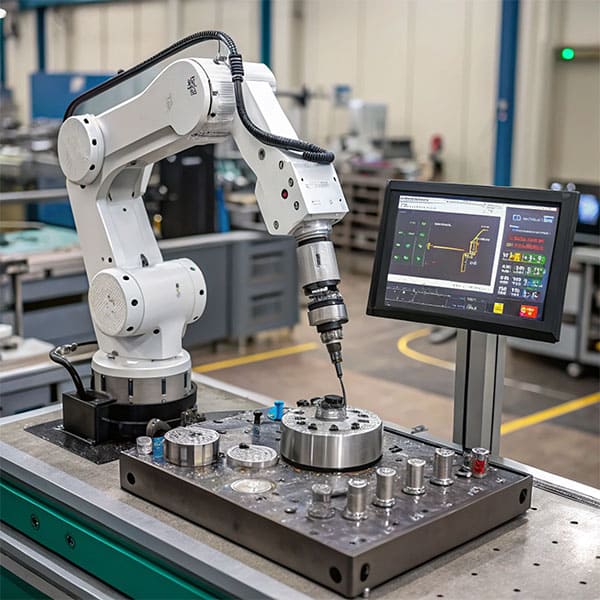
Real-Time Data for Precision Systems
Accelerometers and gyroscopes provide real-time data on motion and orientation, enabling precise control of robotic arms, surgical instruments, or flight paths, ensuring high performance in critical applications.
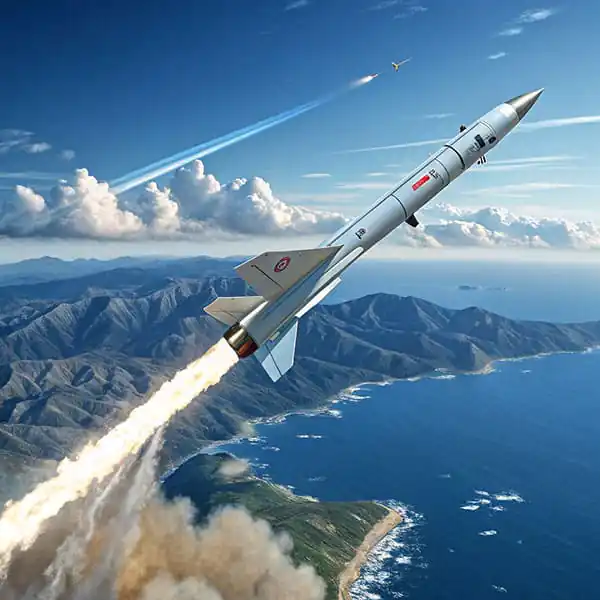
Position and Orientation Tracking
Combining accelerometers and gyroscopes with advanced algorithms, INS systems provide continuous, high-precision tracking of position, velocity, and orientation, even in environments where traditional navigation systems fail.
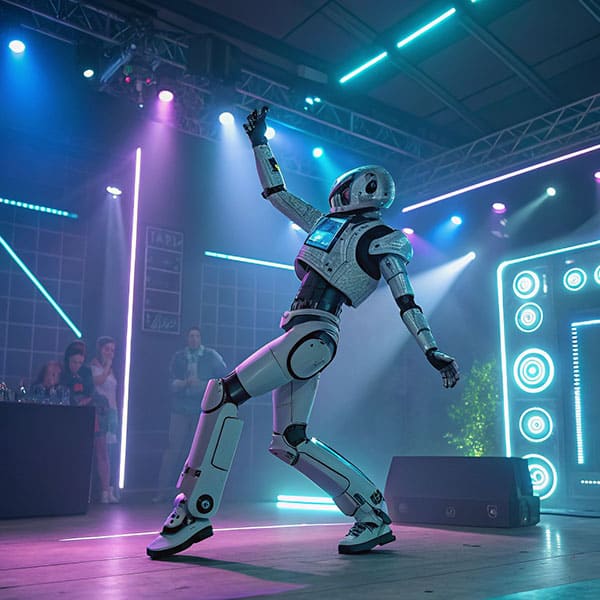
Enhanced Stability and Control
Gyroscopes measure rotational rates and provide real-time feedback to control systems, maintaining balance and stability, thereby improving safety and efficiency in industries like aerospace and robotics.
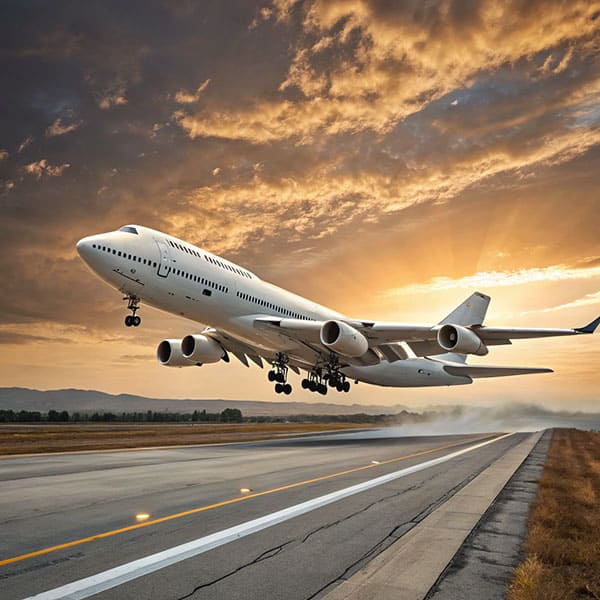
Data-Driven Performance Monitoring
Accelerometers and gyroscopes help monitor vibrations, shocks, and other dynamic forces, allowing early detection of potential issues, improving predictive maintenance, and enhancing overall system reliability.
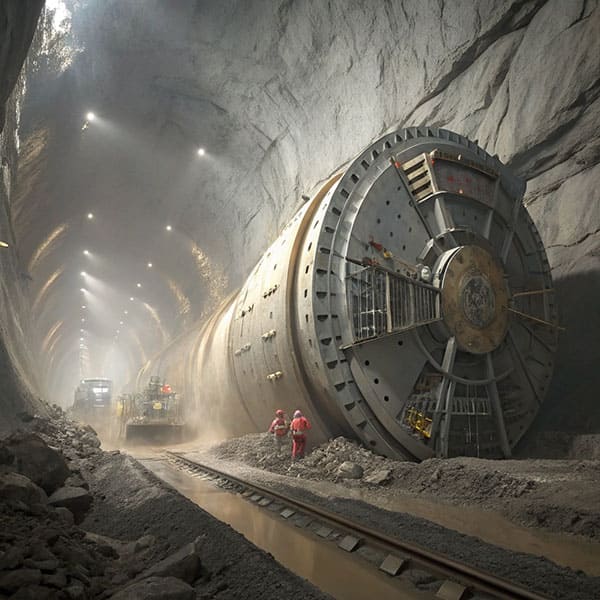
Autonomous Navigation
Inertial navigation systems (INS) combine gyroscopes and accelerometers to provide continuous, self-contained navigation, allowing precise movement tracking and positioning even in GPS-denied environments.
How we work for our customers.
Our workflow is designed to ensure efficiency and quality at every stage of production. From initial consultation and design to manufacturing and final quality checks, each step is meticulously managed to meet the highest standards and customer expectations.
Step1
The products required by the customer.
- Identify Needs: Understand the specific challenges (e.g., motion sensing, position tracking) the product must address.
- Feasibility Study: Evaluate the technical viability and required resources.
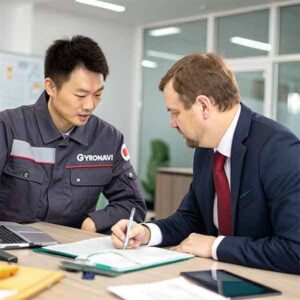
Step2
Design and Prototyping
- System Design: Develop the product architecture, choosing the appropriate sensors and signal processing methods.
- Component Selection: Select sensors and microprocessors based on accuracy and application requirements.
- Prototype: Create the first working model to test functionality and performance.
Step6
After-Sales Support
- Technical Support: Offer troubleshooting and software updates.
- Maintenance Services: Provide ongoing maintenance to ensure product performance.
- Customer Feedback: Use feedback to improve future versions.
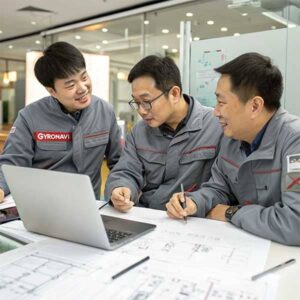
Step3
Testing and Simulation
- Performance Simulation: Use tools to simulate real-world conditions (e.g., temperature, vibration).
- Environmental Testing: Test the product under extreme conditions (e.g., high/low temperatures, pressure).
- Calibration Testing: Ensure sensor accuracy and long-term stability.
.
Step5
Production and Quality Control
- Production Setup: Designing a rational production process and workflow for mass production
- Quality Control: Test products at each stage of production to ensure quality.
- Final Inspection: Ensure each unit meets specifications.
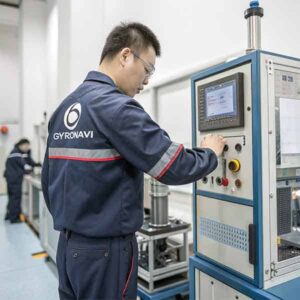
Step4
Refinement and Optimization
- Design Refinement: Improve performance, reduce power consumption, and optimize size.
- Software Optimization: Enhance data processing algorithms to ensure accurate, real-time results.
- Compliance Testing: Meet industry standards (e.g., ISO, CE).
Partial product display. For more products, please contact us
Welcome to Visit Our Factory at any time
Our factory, equipped with advanced machinery and supported by a well-established management system, provides the foundation for producing high-quality products. We invite you to visit and observe our commitment to excellence in every step of production.
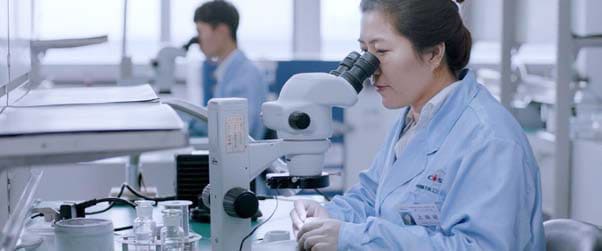
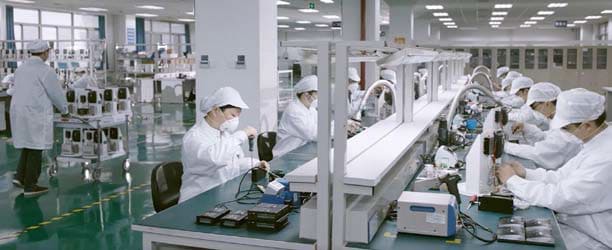
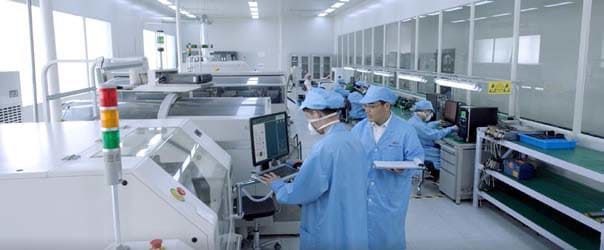
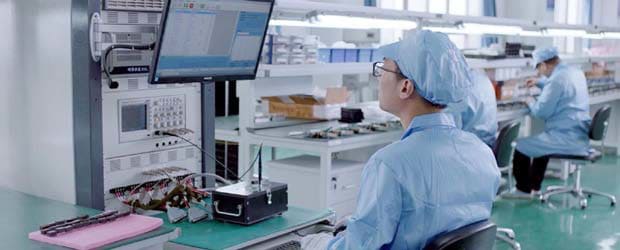
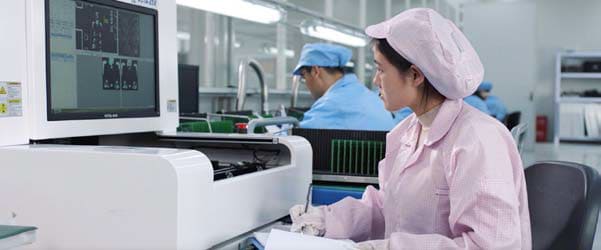
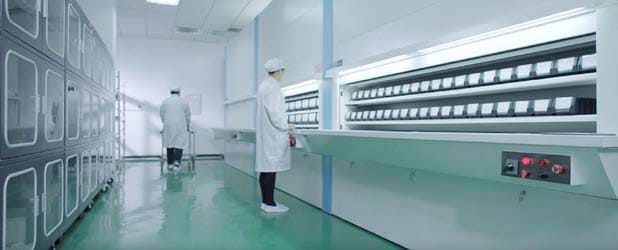
Our products perform exceptionally well in these fields.
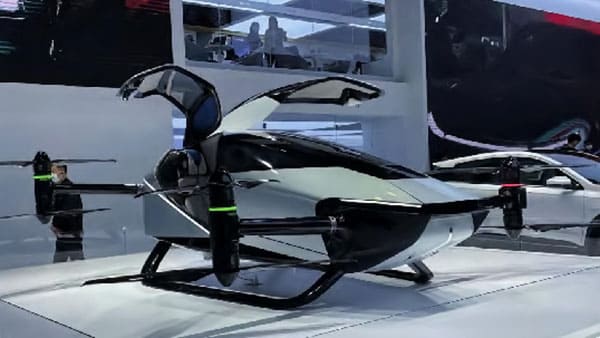
Drone Industry
Our products are widely used in the drone industry, providing precise navigation and stability solutions. Whether for commercial, industrial, or military applications, our advanced sensors and systems enhance the performance and reliability of unmanned aerial vehicles (UAVs).
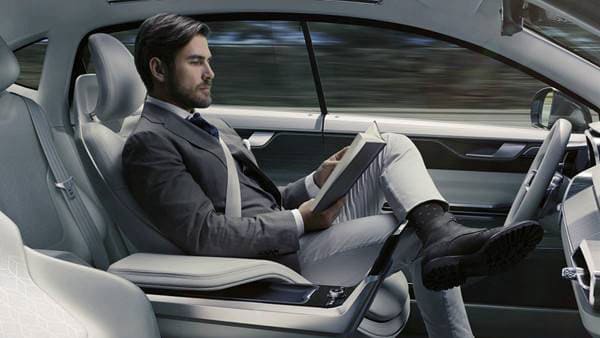
Autonomous Driving Industry
Our products play a crucial role in the autonomous driving industry, providing essential navigation, sensing, and stability solutions. With advanced gyroscopes and inertial measurement units (IMUs), our systems ensure precise control and reliable performance for autonomous vehicles in various environments.
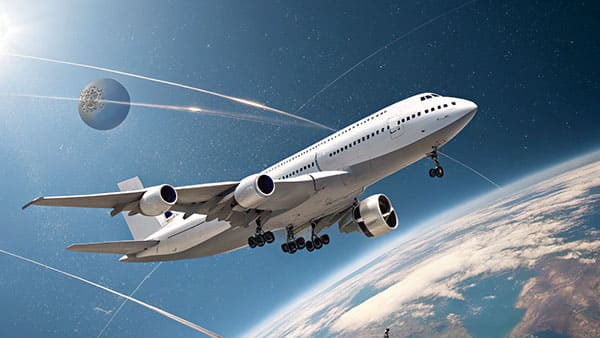
Aerospace Industry
Our products are essential in the aerospace industry, offering high-precision navigation and stability solutions for both spacecraft and satellite systems. With advanced gyroscopes and inertial navigation systems, we provide the reliability needed for critical aerospace applications, ensuring precise performance in even the most demanding conditions.
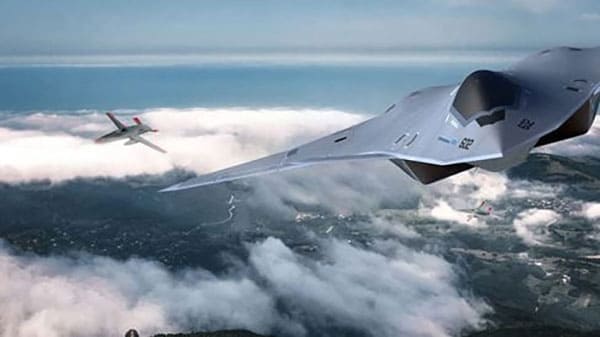
Aviation Industry
Our products are integral to the aviation industry, providing high-precision navigation and stability solutions for aircraft systems. With advanced gyroscopes and inertial measurement units (IMUs), we ensure reliable performance in flight control, navigation, and guidance systems, enhancing safety and operational efficiency.
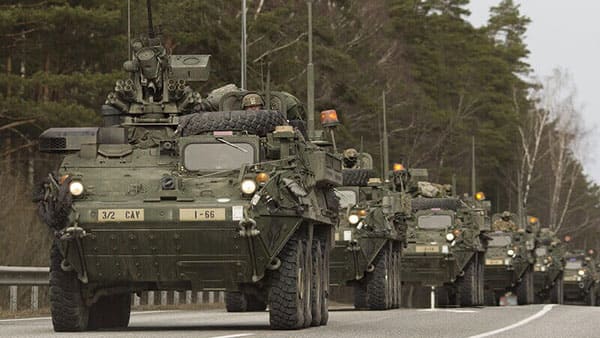
Defense and Military Industry
Our products are critical in the defense and military industry, offering precise navigation, stabilization, and guidance solutions for various military applications. From missile guidance systems to unmanned vehicles, our high-precision gyroscopes and inertial navigation systems ensure reliable performance in demanding and high-risk environments.
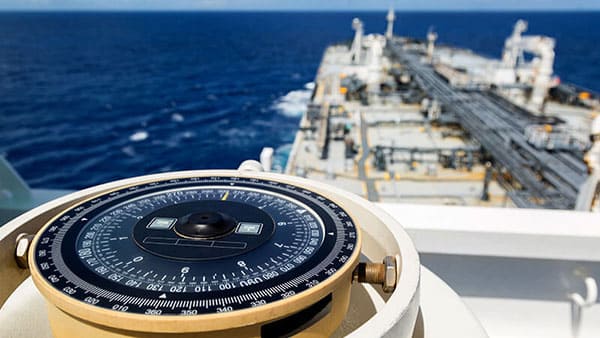
Maritime Navigation and Detection Industry
Our products are vital in the maritime navigation and detection industry, providing precise and reliable solutions for underwater and surface vessels. With advanced gyroscopes and inertial navigation systems, we support accurate positioning, navigation, and detection, ensuring safe and efficient operations in challenging marine environments.
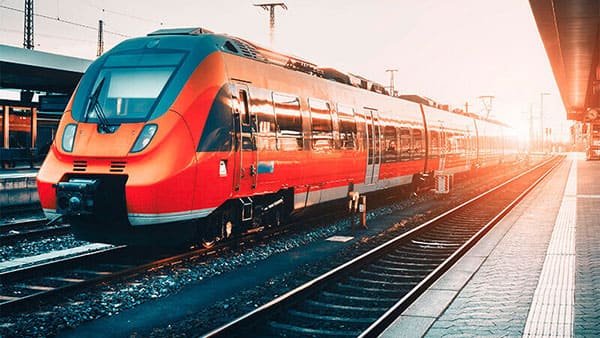
Rail Transit Industry
Our products are essential in the rail transit industry, providing reliable navigation and stability solutions for trains and other rail vehicles. With high-precision gyroscopes and inertial navigation systems, we ensure safe, efficient, and accurate operation of rail systems, supporting both on-board control and infrastructure management.
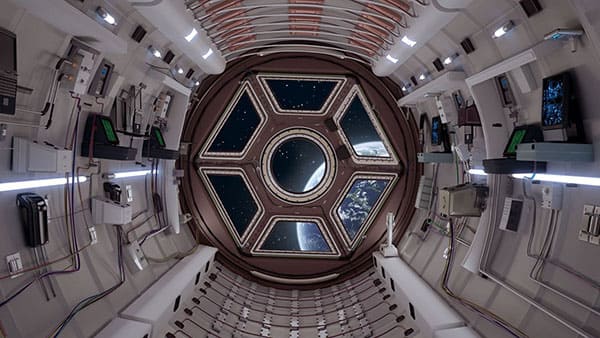
Space Exploration Industry
Our products are crucial in the space exploration industry, offering precise navigation and orientation solutions for spacecraft, rovers, and satellites. With advanced gyroscopes and inertial measurement units (IMUs), we ensure reliable performance in the extreme conditions of space, supporting accurate positioning and stability during missions to explore the universe.
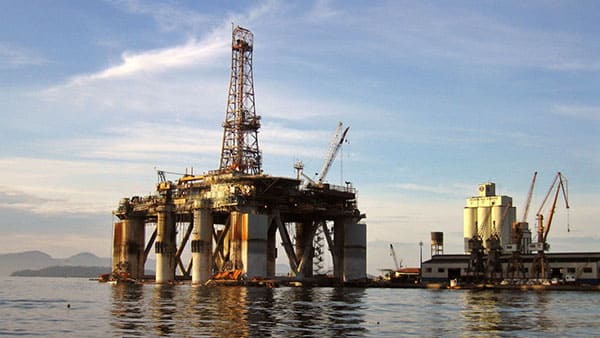
Geological Exploration Industry
Our products play a key role in the geological exploration industry, providing accurate and reliable navigation and measurement solutions for surveying equipment, drilling systems, and exploration vehicles. With high-precision gyroscopes and inertial navigation systems, we ensure precise positioning and stability, even in challenging and remote environments.
After-Sales Service
At GYRONAVI, we understand that reliability and precision are crucial in the field of inertial navigation systems. That’s why we not only provide cutting-edge products but also offer a robust after-sales support structure designed to keep your systems running smoothly, ensuring uninterrupted business operations. With our 7 days, 12 hours service and 3-year warranty, you are not just buying products — you’re securing a long-term partnership for continuous support and success.
Why Choose Our After-Sales Service?
- 12-Hour Technical Issue Resolution: We guarantee to resolve your product’s technical issues within 12 hours.
- 3-Year Warranty: All products come with a comprehensive 3-year warranty for peace of mind.
- Expert Technical Support: Our team is ready to assist with any technical queries or issues regarding our products.
- Global Service Network: We provide tailored support with fast response times, no matter where you’re located.
- Spare Parts Availability: A well-stocked inventory ensures quick replacement of parts to minimize downtime.
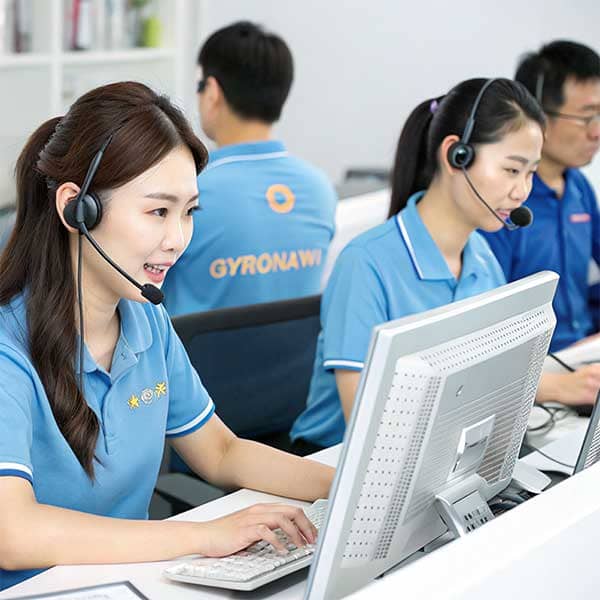
FAQs
What is the difference between an accelerometer and a gyroscope?
An accelerometer measures linear acceleration in one or more directions, which can be used to detect motion, vibrations, or changes in speed. It detects how quickly an object is speeding up or slowing down along an axis. A gyroscope, on the other hand, measures rotational motion around an axis. It helps in determining orientation or angular velocity, providing stability and direction for a system. Both sensors are often used together in applications requiring precise motion tracking and navigation.
How do fiber optic gyroscopes (FOGs) compare to traditional mechanical gyroscopes?
Fiber optic gyroscopes (FOGs) are more accurate, reliable, and stable than traditional mechanical gyroscopes. FOGs use the interference of light traveling through a fiber-optic coil to measure rotation, avoiding the mechanical parts that wear out in conventional gyroscopes. This results in higher precision, no moving parts, and better performance in harsh environments (e.g., high vibrations, temperature extremes). They are widely used in aerospace and marine applications.
What is a laser gyroscope, and how does it differ from fiber optic gyroscopes?
A laser gyroscope uses a laser beam and a rotating mirror to measure angular velocity. The interference pattern of the light as it travels around a ring is compared to determine the rotation. Laser gyroscopes generally offer higher precision than fiber optic gyroscopes but are more complex and expensive. Fiber optic gyroscopes, by contrast, are simpler and more cost-effective for many industrial and commercial uses, especially in environments where size and weight matter.
How does an inertial navigation system (INS) work?
An inertial navigation system (INS) combines accelerometers and gyroscopes to calculate the position, orientation, and velocity of a moving object without the need for external reference points (like GPS). The accelerometers measure linear accelerations, while the gyroscopes measure rotational movements. This data is processed to determine the object’s exact position and trajectory over time, making INS ideal for situations where GPS signals are unavailable or unreliable, such as underwater, underground, or in remote areas.。
What are the key factors to consider when selecting an accelerometer for my application?
When selecting an accelerometer, consider the following factors:
- Range: Ensure the accelerometer can measure the expected range of acceleration in your application.
- Sensitivity: The sensor’s ability to detect small changes in acceleration.
- Noise performance: Look for low noise levels for precision in measurements.
- Power consumption: Choose an accelerometer that balances power consumption and performance for your system.
- Size and weight: Consider the physical space available for the sensor.
- Environmental conditions: Ensure the accelerometer can withstand factors like temperature extremes, humidity, and vibration.
What applications typically use fiber optic gyroscopes?
Fiber optic gyroscopes (FOGs) are commonly used in applications requiring high accuracy and reliability, such as:
- Aerospace: For aircraft navigation and attitude control.
- Marine: For ship navigation, stabilizers, and guidance systems.
- Military: In missile guidance, unmanned vehicles, and weapon systems.
- Autonomous vehicles: To improve navigation systems by providing real-time orientation data.
FOGs are ideal for situations where size, weight, and high precision are essential.
How do I integrate an inertial navigation system into my application?
Integration of an inertial navigation system (INS) typically involves connecting the system to a host device, such as a computer, vehicle control system, or robotic platform. The INS provides data on velocity, position, and orientation, which must be processed to achieve the desired output. This may involve software development to handle sensor fusion, real-time processing, and calibration. Ensure your INS is properly calibrated before use to avoid accumulated errors in long-term applications. Many modern INS systems come with integration kits to simplify the process.
What is the typical lifespan of a fiber optic gyroscope?
Fiber optic gyroscopes are known for their longevity. With no moving parts, they generally have a lifespan of over 10 years with proper maintenance. However, the actual lifespan can depend on factors such as the operating environment (temperature, humidity, vibrations), the specific model, and usage conditions. Regular calibration and monitoring can help extend the life of a FOG system and ensure continued accuracy over time.
Get Your Customized Motion Control Solutions Today
Looking for high-performance accelerometers, gyroscopes, or inertial navigation systems? Our expert solutions are designed to meet your precise motion and attitude control needs. Fill out the form below, and our team will provide you with the perfect solution tailored to your application