Quartz Accelerometer
Reliable Quartz Accelerometer and Solutions
Our products are known for their high precision, stability, and reliability.With a professional team and years of experience,
Standard Products and Custom Solutions Offered
Quartz accelerometers, including two primary types—Quartz Flexible Accelerometer (QFA) and Quartz Flexural Beam Accelerometer (QBA)—are crucial for high-precision measurements in modern inertial navigation systems. These accelerometers offer exceptional accuracy and stability, making them indispensable for applications in aerospace, defense, robotics, and more.
In the ever-evolving world of technology, precision and reliability are paramount, especially in critical applications such as aerospace, defense, oil exploration, robotics, and automation. At GYRONAVI, we specialize in delivering high-quality, high-precision, and highly stable quartz accelerometers, essential components for your inertial navigation systems.
Our quartz accelerometer are engineered to meet the stringent requirements of mission-critical applications, where accuracy and durability are non-negotiable. Whether you are developing guidance systems for spacecraft, performing seismic surveys in remote oil fields, or designing advanced robotics systems, our products deliver the performance you need to stay ahead in your field.
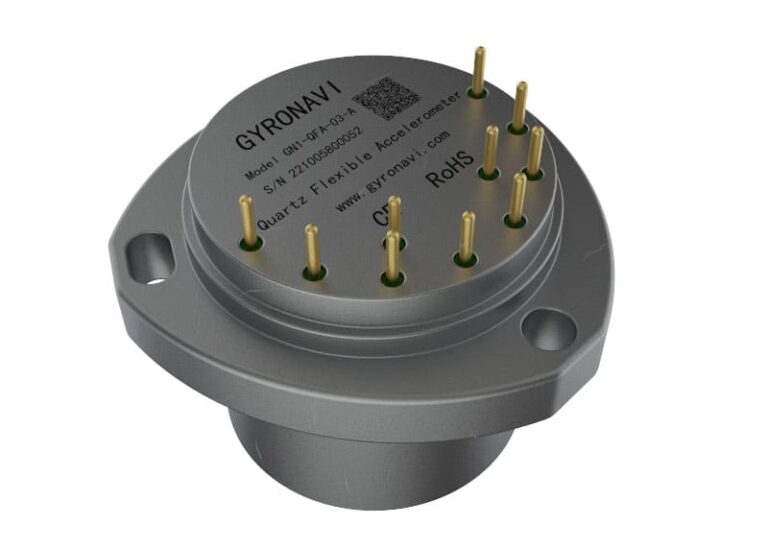
Request More Details today to see how our products can support your projects.
Partial product display. For more products, please contact us
Product Features
- Analog output
- Excellent repeatability
- Temperature sensor can be integrated based on requirements
- Wide load resistance range
- Triangular precision mounting flange
- Successfully used in satellite control, microgravity measurement, and spaceship reentry capsule main inertial navigation.
Product Overview
The quartz flexible accelerometer(QFA) operates based on the principles of inertia, using quartz flexible supports along with advanced electronic technology to create a precise instrument. In a force balance state, the output of the accelerometer is directly proportional to the input acceleration. By measuring the output of the accelerometer, the input acceleration can be accurately calculated. It features a high output impedance with a current output form, allowing users to select the necessary sampling resistance without affecting system stability.
Currently, our company’s quartz flexible accelerometers have been developed into a series of products. These range from high-precision μg-level GN1-QFA-02 accelerometers used for satellite microgravity measurements, to low-cost, environmentally-resistant GN1-QFA-T12 accelerometers used for oil drilling, with over a dozen types available. They are widely used in various fields such as aerospace, aviation, shipbuilding, weaponry, petroleum, and geotechnical engineering, providing signals for navigation, guidance, control, leveling, and monitoring systems.
Main Technical Specifications
Parameter | GN1-QFA-02-A | GN1-QFA-02-B |
---|---|---|
Range (g) | ±20 | ±20 |
Bias (mg) | ≤5 | ≤5 |
Temperature Coefficient (μg/°C) | ≤10 | ≤30 |
Monthly Repeatability (1σ, μg) | ≤10 | ≤30 |
Scale Factor (mA/g) | 1.2~1.6 | 1.2~1.6 |
Temperature Coefficient (10¯6/℃) | ≤10 | ≤50 |
Monthly Repeatability (1σ/10¯6) | ≤10 | ≤40 |
Second Order Non-linearity (μg/g²) | ≤10 | ≤40 |
Threshold (μg) | ≤1 | ≤5 |
Resolution (μg) | ≤1 | ≤ 5 |
Input Voltage (V) | ±12 ~ ±18 | ±12 ~ ±18 |
Operating Temperature (°C) | -45 ~ +80 | -45 ~ +80 |
Storage Temperature (°C) | -55 ~ +80 | -55 ~ +80 |
Dimensions (mm) | Ф25.4×30 | Ф25.4×30 |
Weight (g) | ≤70 | ≤70 |
Vibration(g,Hz) | 15g, 20Hz~2000Hz, Sine | 15g, 20Hz~2000Hz, Sine |
Shock(g,ms) | 100g, 8ms~12ms, Half Sine | 100g, 8ms~12ms, Half Sine |
Product Features
- Wide input range.
- Analog output.
- Excellent repeatability.
- Temperature sensor can be integrated based on requirements.
- Wide load resistance range.
- Triangular precision mounting flange.
- Excellent impact and vibration resistance.
Product Overview
The quartz flexible accelerometer(QFA) operates based on the principles of inertia, using quartz flexible supports along with advanced electronic technology to create a precise instrument. In a force balance state, the output of the accelerometer is directly proportional to the input acceleration. By measuring the output of the accelerometer, the input acceleration can be accurately calculated. It features a high output impedance with a current output form, allowing users to select the necessary sampling resistance without affecting system stability.
Currently, our company’s quartz flexible accelerometers have been developed into a series of products. These range from high-precision μg-level GN1-QFA-02 accelerometers used for satellite microgravity measurements, to low-cost, environmentally-resistant GN1-QFA-T12 accelerometers used for oil drilling, with over a dozen types available. They are widely used in various fields such as aerospace, aviation, shipbuilding, weaponry, petroleum, and geotechnical engineering, providing signals for navigation, guidance, control, leveling, and monitoring systems.
Main Technical Specifications
Parameter | GN1-QFA-03-A | GN1-QFA-03-B |
---|---|---|
Range (g) | ±70 | ±40 |
Bias (mg) | ≤5 | ≤5 |
Temperature Coefficient (μg/°C) | ≤30 | ≤50 |
Monthly Repeatability (1σ, μg) | ≤30 | ≤60 |
Scale Factor (mA/g) | 0.9~1.3 | 0.9~1.3 |
Temperature Coefficient (10¯6/℃) | ≤50 | ≤80 |
Monthly Repeatability (1σ/10¯6) | ≤40 | ≤60 |
Second Order Non-linearity (μg/g²) | ≤40 | ≤40 |
Threshold (μg) | ≤5 | ≤5 |
Resolution (μg) | ≤5 | ≤ 5 |
Input Voltage (V) | ±12 ~ ±18 | ±12 ~ ±18 |
Operating Temperature (°C) | -45 ~ +80 | -45 ~ +80 |
Storage Temperature (°C) | -55 ~ +80 | -55 ~ +80 |
Dimensions (mm) | Ф25.4×30 | Ф25.4×30 |
Weight (g) | ≤80 | ≤80 |
Vibration(g,Hz) | 20g, 20Hz~2000Hz, Sine | 20g, 20Hz~2000Hz, Sine |
Shock(g,ms) | 200g, 8ms~12ms, Half Sine | 200g, 8ms~12ms, Half Sine |
Product Features
- Excellent repeatability.
- Analog output.
- Built-in digital temperature sensor.
- Wide load resistance range.
- Triangular precision mounting flange.
- Successfully used in next-generation weapon inertial navigation systems.
Product Overview
The quartz flexible accelerometer(QFA) operates based on the principles of inertia, using quartz flexible supports along with advanced electronic technology to create a precise instrument. In a force balance state, the output of the accelerometer is directly proportional to the input acceleration. By measuring the output of the accelerometer, the input acceleration can be accurately calculated. It features a high output impedance with a current output form, allowing users to select the necessary sampling resistance without affecting system stability.
Currently, our company’s quartz flexible accelerometers have been developed into a series of products. These range from high-precision μg-level GN1-QFA-02 accelerometers used for satellite microgravity measurements, to low-cost, environmentally-resistant GN1-QFA-T12 accelerometers used for oil drilling, with over a dozen types available. They are widely used in various fields such as aerospace, aviation, shipbuilding, weaponry, petroleum, and geotechnical engineering, providing signals for navigation, guidance, control, leveling, and monitoring systems.
Main Technical Specifications
Parameter | GN1-QFA-05-A | GN1-QFA-05-B |
---|---|---|
Range (g) | ±40 | ±20 |
Bias (mg) | ≤5 | ≤5 |
Temperature Coefficient (μg/°C) | ≤10 | ≤20 |
Monthly Repeatability (1σ, μg) | ≤10 | ≤20 |
Scale Factor (mA/g) | 1.2~1.6 | 1.2~1.6 |
Temperature Coefficient (10¯6/℃) | ≤10 | ≤30 |
Monthly Repeatability (1σ/10¯6) | ≤10 | ≤30 |
Second Order Non-linearity (μg/g²) | ≤10 | ≤30 |
Threshold (μg) | ≤1 | ≤5 |
Resolution (μg) | ≤1 | ≤5 |
Input Voltage (V) | ±12 ~ ±18 | ±12 ~ ±18 |
Operating Temperature (°C) | -45 ~ +80 | -45 ~ +80 |
Storage Temperature (°C) | -55 ~ +80 | -55 ~ +80 |
Dimensions (mm) | Ф25.4×29 | Ф25.4×29 |
Weight (g) | ≤75 | ≤75 |
Vibration(g,Hz) | 15g, 20Hz~2000Hz, Sine | 15g, 20Hz~2000Hz, Sine |
Shock(g,ms) | 100g, 8ms~12ms, Half Sine | 100g, 8ms~12ms, Half Sine |
Product Features
- Analog output.
- Excellent repeatability.
- Temperature sensor can be integrated based on requirements.
- Wide load resistance range.
- Square precision mounting flange.
- Successfully implemented in engineering applications.
Product Overview
The quartz flexible accelerometer(QFA) operates based on the principles of inertia, using quartz flexible supports along with advanced electronic technology to create a precise instrument. In a force balance state, the output of the accelerometer is directly proportional to the input acceleration. By measuring the output of the accelerometer, the input acceleration can be accurately calculated. It features a high output impedance with a current output form, allowing users to select the necessary sampling resistance without affecting system stability.
Currently, our company’s quartz flexible accelerometers have been developed into a series of products. These range from high-precision μg-level GN1-QFA-02 accelerometers used for satellite microgravity measurements, to low-cost, environmentally-resistant GN-QFA-T12 accelerometers used for oil drilling, with over a dozen types available. They are widely used in various fields such as aerospace, aviation, shipbuilding, weaponry, petroleum, and geotechnical engineering, providing signals for navigation, guidance, control, leveling, and monitoring systems.
Main Technical Specifications
Parameter | GN1-QFA-07-A | GN1-QFA-07-B |
---|---|---|
Range (g) | ±20 | ±20 |
Bias (mg) | ≤5 | ≤5 |
Temperature Coefficient (μg/°C) | ≤30 | ≤50 |
Monthly Repeatability (1σ, μg) | ≤30 | ≤50 |
Scale Factor (mA/g) | 1.2~1.6 | 1.2~1.6 |
Temperature Coefficient (10¯6/℃) | ≤30 | ≤80 |
Monthly Repeatability (1σ/10¯6) | ≤30 | ≤50 |
Second Order Non-linearity (μg/g²) | ≤15 | ≤40 |
Threshold (μg) | ≤5 | ≤5 |
Resolution (μg) | ≤5 | ≤ 5 |
Input Voltage (V) | ±12 ~ ±18 | ±12 ~ ±18 |
Operating Temperature (°C) | -45 ~ +80 | -45 ~ +80 |
Storage Temperature (°C) | -55 ~ +80 | -55 ~ +80 |
Dimensions (mm) | Ф25.4×32 | Ф25.4×32 |
Weight (g) | ≤70 | ≤70 |
Vibration(g,Hz) | 15g, 20Hz~2000Hz, Sine | 15g, 20Hz~2000Hz, Sine |
Shock(g,ms) | 100g, 8ms~12ms, Half Sine | 100g, 8ms~12ms, Half Sine |
Product Features
- Small size and light weight.
- Analog output.
- Wide load resistance range.
- Square precision mounting flange.
- Successfully used in UAVs and petroleum pipelines.
Product Overview
The quartz flexible accelerometer(QFA) operates based on the principles of inertia, using quartz flexible supports along with advanced electronic technology to create a precise instrument. In a force balance state, the output of the accelerometer is directly proportional to the input acceleration. By measuring the output of the accelerometer, the input acceleration can be accurately calculated. It features a high output impedance with a current output form, allowing users to select the necessary sampling resistance without affecting system stability.
Currently, our company’s quartz flexible accelerometers have been developed into a series of products. These range from high-precision μg-level GN1-QFA-2 accelerometers used for satellite microgravity measurements, to low-cost, environmentally-resistant GN-QFA-T12 accelerometers used for oil drilling, with over a dozen types available. They are widely used in various fields such as aerospace, aviation, shipbuilding, weaponry, petroleum, and geotechnical engineering, providing signals for navigation, guidance, control, leveling, and monitoring systems.
Main Technical Specifications
Parameter | GN1-QFA-08-A | GN1-QFA-08-B |
---|---|---|
Range (g) | ±40 | ±20 |
Bias (mg) | ≤5 | ≤5 |
Temperature Coefficient (μg/°C) | ≤40 | ≤50 |
Monthly Repeatability (1σ, μg) | ≤40 | ≤80 |
Scale Factor (mA/g) | 0.9~1.3 | 0.9~1.3 |
Temperature Coefficient (10¯6/℃) | ≤60 | ≤60 |
Monthly Repeatability (1σ/10¯6) | ≤40 | ≤80 |
Second Order Non-linearity (μg/g²) | ≤50 | ≤50 |
Threshold (μg) | ≤5 | ≤5 |
Resolution (μg) | ≤5 | ≤ 5 |
Input Voltage (V) | ±12 ~ ±18 | ±12 ~ ±18 |
Operating Temperature (°C) | -45 ~ +80 | -45 ~ +80 |
Storage Temperature (°C) | -55 ~ +80 | -55 ~ +80 |
Dimensions (mm) | Ф18.2×23.6 | Ф18.2×23.6 |
Weight (g) | ≤35 | ≤35 |
Vibration(g,Hz) | 15g, 20Hz~2000Hz, Sine | 15g, 20Hz~2000Hz, Sine |
Shock(g,ms) | 100g, 8ms~12ms, Half Sine | 100g, 8ms~12ms, Half Sine |
Product Features
- Small size and light weight.
- Analog output.
- Excellent repeatability.
- Good impact and vibration resistance.
- Wide load resistance range.
- Square precision mounting flange.
- Wide operating temperature range.
Product Overview
The quartz flexible accelerometer (QFA)operates based on the principles of inertia, using quartz flexible supports along with advanced electronic technology to create a precise instrument. In a force balance state, the output of the accelerometer is directly proportional to the input acceleration. By measuring the output of the accelerometer, the input acceleration can be accurately calculated. It features a high output impedance with a current output form, allowing users to select the necessary sampling resistance without affecting system stability.
Currently, our company’s quartz flexible accelerometers have been developed into a series of products. These range from high-precision μg-level GN1-QFA-02 accelerometers used for satellite microgravity measurements, to low-cost, environmentally-resistant GN1-QFA-T12 accelerometers used for oil drilling, with over a dozen types available. They are widely used in various fields such as aerospace, aviation, shipbuilding, weaponry, petroleum, and geotechnical engineering, providing signals for navigation, guidance, control, leveling, and monitoring systems.
Main Technical Specifications
Parameter | GN1-QFA-06-A | GN1-QFA-06-B |
---|---|---|
Range (g) | ±30 | ±10 |
Bias (mg) | ≤8 | ≤10 |
Temperature Coefficient (μg/°C) | ≤40 | ≤100 |
Monthly Repeatability (1σ, μg) | ≤50 | ≤100 |
Scale Factor (mA/g) | 1.0~1.6 | 2.5~3.5 |
Temperature Coefficient (10¯6/℃) | ≤80 | ≤100 |
Monthly Repeatability (1σ/10¯6) | ≤80 | ≤100 |
Second Order Non-linearity (μg/g²) | ≤40 | ≤60 |
Threshold (μg) | ≤5 | ≤10 |
Resolution (μg) | ≤5 | ≤ 10 |
Input Voltage (V) | ±12 ~ ±18 | ±12 ~ ±18 |
Operating Temperature (°C) | -45 ~ +100 | -45 ~ +100 |
Storage Temperature (°C) | -55 ~ +120 | -55 ~ +120 |
Dimensions (mm) | Ф25×25 | Ф25×25 |
Weight (g) | ≤50 | ≤50 |
Vibration(g,Hz) | 25g, 30Hz~500Hz, Sine | 25g, 30Hz~500Hz, Sine |
Shock(g,ms) | 500g, 1ms~3ms, Half Sine | 500g, 1ms~3ms, Half Sine |
Product Features
- Resistant to harsh environments.
- Analog output.
- Wide load resistance range.
- Square mounting flange options.
- Successfully used in petroleum drilling measurement systems.
Product Overview
The quartz flexible accelerometer(QFA) operates based on the principles of inertia, using quartz flexible supports along with advanced electronic technology to create a precise instrument. In a force balance state, the output of the accelerometer is directly proportional to the input acceleration. By measuring the output of the accelerometer, the input acceleration can be accurately calculated. It features a high output impedance with a current output form, allowing users to select the necessary sampling resistance without affecting system stability.
Currently, our company’s quartz flexible accelerometers have been developed into a series of products. These range from high-precision μg-level GN1-QFA-02 accelerometers used for satellite microgravity measurements, to low-cost, environmentally-resistant GN1-QFA-12 accelerometers used for oil drilling, with over a dozen types available. They are widely used in various fields such as aerospace, aviation, shipbuilding, weaponry, petroleum, and geotechnical engineering, providing signals for navigation, guidance, control, leveling, and monitoring systems.
Main Technical Specifications
Parameter | GN1-QFA-T10-A | GN1-QFA-T10-B |
---|---|---|
Range (g) | ±20 | ±20 |
Bias (mg) | ≤20 | ≤30 |
Temperature Coefficient (μg/°C) | ≤150 | ≤150 |
Monthly Repeatability (1σ, μg) | ≤100 | ≤200 |
Scale Factor (mA/g) | 2.2~3.5 | 2.2~3.5 |
Temperature Coefficient (10¯6/℃) | ≤200 | ≤300 |
Monthly Repeatability (1σ/10¯6) | ≤100 | ≤200 |
Second Order Non-linearity (μg/g²) | ≤100 | ≤150 |
Threshold (μg) | ≤10 | ≤15 |
Resolution (μg) | ≤10 | ≤ 15 |
Input Voltage (V) | ±12 ~ ±18 | ±12 ~ ±18 |
Operating Temperature (°C) | -45 ~ +125 | -45 ~ +180 |
Storage Temperature (°C) | -55 ~ +120 | -55 ~ +120 |
Dimensions (mm) | Ф18.8×21 | Ф18.8×21 |
Weight (g) | ≤25 | ≤25 |
Vibration(g,Hz) | 20g, 10Hz~500Hz, Sine | 20g, 10Hz~500Hz, Sine |
Shock(g,ms) | 1000g, 0.5ms Half Sine | 1000g, 0.5ms Half Sine |
Product Features
- Resistant to harsh environments.
- Analog output.
- Wide load resistance range.
- Round or square mounting flange options.
- Temperature model provided for temperature compensation.
- Successfully used in petroleum drilling measurement systems.
Product Overview
The quartz flexible accelerometer(QFA) operates based on the principles of inertia, using quartz flexible supports along with advanced electronic technology to create a precise instrument. In a force balance state, the output of the accelerometer is directly proportional to the input acceleration. By measuring the output of the accelerometer, the input acceleration can be accurately calculated. It features a high output impedance with a current output form, allowing users to select the necessary sampling resistance without affecting system stability.
Currently, our company’s quartz flexible accelerometers have been developed into a series of products. These range from high-precision μg-level GN1-QFA-02 accelerometers used for satellite microgravity measurements, to low-cost, environmentally-resistant GN-QFA-T12 accelerometers used for oil drilling, with over a dozen types available. They are widely used in various fields such as aerospace, aviation, shipbuilding, weaponry, petroleum, and geotechnical engineering, providing signals for navigation, guidance, control, leveling, and monitoring systems.
Main Technical Specifications
Parameter | GN1-QFA-T12-A | GN1-QFA-T12-B |
---|---|---|
Range (g) | ±10 | ±10 |
Bias (mg) | ≤20 | ≤20 |
Temperature Coefficient (μg/°C) | ≤150 | ≤150 |
Monthly Repeatability (1σ, μg) | ≤100 | ≤150 |
Scale Factor (mA/g) | 2.2~3.5 | 2.2~3.5 |
Temperature Coefficient (10¯6/℃) | ≤150 | ≤300 |
Monthly Repeatability (1σ/10¯6) | ≤100 | ≤150 |
Second Order Non-linearity (μg/g²) | ≤100 | ≤150 |
Threshold (μg) | ≤10 | ≤15 |
Resolution (μg) | ≤10 | ≤ 15 |
Input Voltage (V) | ±12 ~ ±18 | ±12 ~ ±18 |
Operating Temperature (°C) | -45 ~ +125 | -45 ~ +170 |
Storage Temperature (°C) | -55 ~ +120 | -55 ~ +120 |
Dimensions (mm) | Ф25×25 | Ф25×25 |
Weight (g) | ≤60 | ≤60 |
Vibration(g,Hz) | 20g, 10Hz~2000Hz, Sine | 20g, 10Hz~2000Hz, Sine |
Shock(g,ms) | 1000g, 0.5ms Half Sine | 1000g, 0.5ms Half Sine |
Product Features
- Large measurement range
- Small size
- High precision
- Low power consumption
- Short startup time
- Shock and vibration resistance
- Stable performance with high reliability
Product Overview
The quartz beam accelerometer(QBA) is a new type of solid-state digital output accelerometer that offers advantages such as a wide measurement range, small size, high precision, low power consumption, short startup time, shock and vibration resistance, and high reliability.we pride ourselves on offering cutting-edge inertial navigation solutions. Our quartz beam accelerometer products are designed with advanced technology and rigorous testing standards to ensure they meet the highest industry demands. With years of experience in accelerometer and gyroscope manufacturing, we are committed to delivering reliable, innovative, and customizable solutions that help optimize the performance of your systems.
Main Technical Specifications
Parameter | GN1-QBA-100-A | GN1-QBA-100-B |
---|---|---|
Measurement Range(g) | ±70 | ±70 |
Zero Bias(mg)∗ | ≤5 | ≤5 |
Zero Bias Monthly Repeatability (1σ,μg)∗ | <100 | <100 |
Scale Factor(Hz/g )∗ | 56 | 80 |
Scale Factor Monthly(ppm) Repeatability (1σ)∗ | <50 | <50 |
Second Order Non-linearity Coefficient(μg/g²)∗ | <80 | <80 |
Second Order Non-linearity Monthly Repeatability (1σ,μg/g²) | <50 | <50 |
Bandwidth(Hz)∗ | >400 | >400 |
Resolution(μg)∗ | <10 | <10 |
Vibration | 5g rms 20Hz~2000Hz | 5g rms 20Hz~2000Hz |
Shock | 200g, 2ms, Half Sine Wave | 200g, 2ms, Half Sine Wave |
Operating Temperature(°C ) | -45~ +85 | -45 ~ +85 |
Natural Frequency(Hz)∗ | 950+ 50 | 950+ 50 |
Operating Voltage(VDC) | 15 ± 1 | 15V ± 1 |
Temperature Sensor Output∗ | @25°C: 40kHz ± 2%, Temperature Coefficient: -29.6×10⁻⁶/°C (+2%) | @25°C: 40kHz ± 2%, Temperature Coefficient: -29.6×10⁻⁶/°C (+2%) |
Power Consumption(mW) | ≤75 | ≤75 |
Dimensions (mm) | 22 x 22 x 14/φ22×14 | 17 x 17 x 11/φ17×11 |
Weight (g) | 22 | 11 |
Remarks:
Parameters marked with “*” are tested under the following conditions: Constant temperature of +55°C, and a voltage of ±15VDC.
Welcome to Visit Our Factory at any time
Our factory, equipped with advanced machinery and supported by a well-established management system, provides the foundation for producing high-quality products. We invite you to visit and observe our commitment to excellence in every step of production.
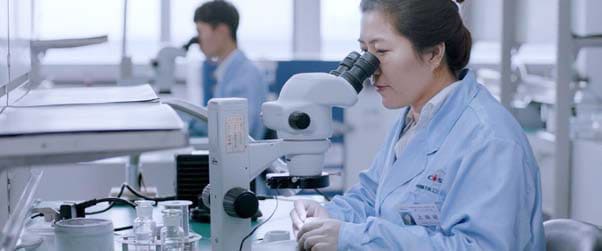
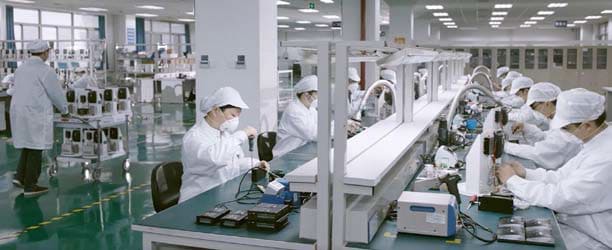
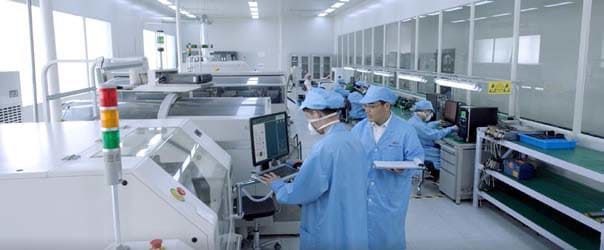
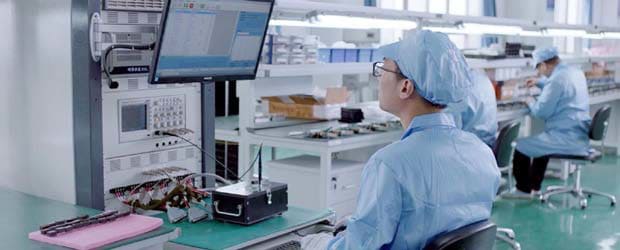
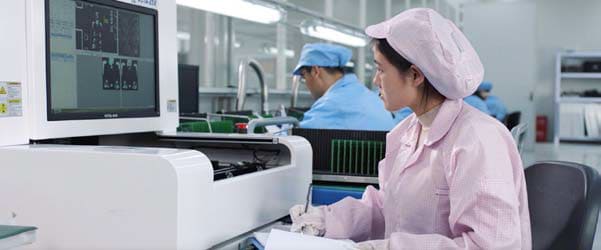
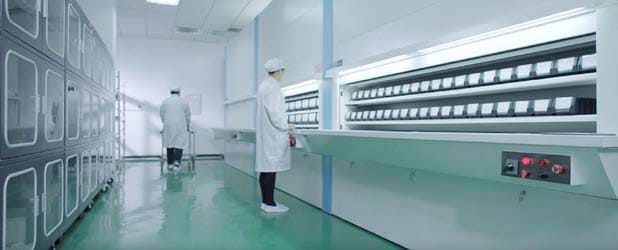
More details you need to know about Quartz Accelerometers
Advantages of Quartz Accelerometers
High Accuracy and Precision: Quartz accelerometers are widely recognized for their high accuracy and low drift, even over long periods. The piezoelectric behavior of quartz is highly predictable, which results in highly repeatable measurements. This makes them suitable for applications where precision is critical, such as in aerospace and automotive industries.
Wide Temperature Range: Quartz accelerometers can operate in extreme temperature conditions ranging from -50°C to +200°C (or more depending on the specific model). Their stable performance in such environments makes them ideal for use in harsh environments where other types of accelerometers may fail.
Long-Term Stability: The piezoelectric characteristics of quartz crystals remain stable over time. This contributes to the long-term reliability of the sensor, reducing the need for frequent recalibration, and making quartz accelerometers suitable for applications that require extended operational lifespans.
Low Power Consumption: Quartz accelerometers are generally designed to consume very little power, making them ideal for battery-operated systems where power conservation is crucial, such as in remote monitoring and portable devices.
.
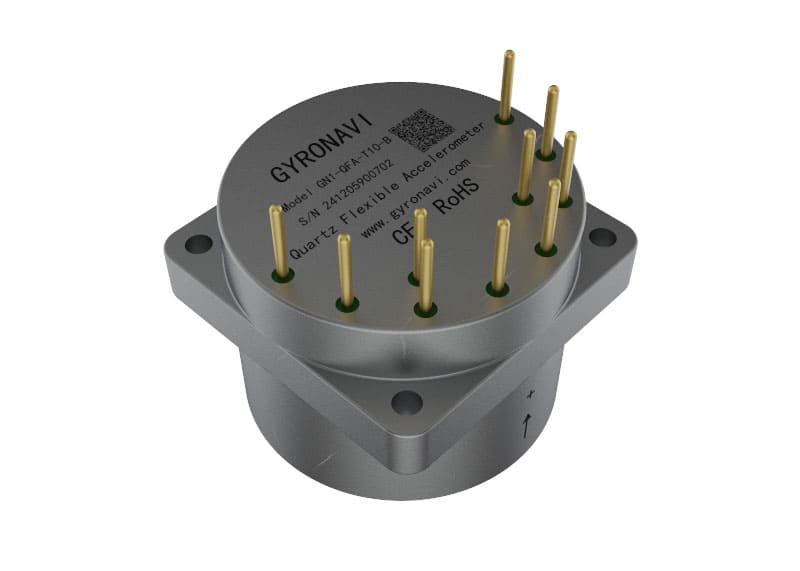
Applications of Quartz Accelerometers
Aerospace: Quartz accelerometers are used in spacecraft and aircraft to measure vibrations, shocks, and movements during flight or testing. These sensors provide crucial data for system monitoring and safety assessments.
Automotive: In the automotive industry, quartz accelerometers are used for crash testing, vehicle stability control systems, and to monitor the performance of critical components under acceleration. Their accuracy ensures that data from safety testing is reliable.
Industrial Machinery: Quartz accelerometers are used to monitor vibrations in industrial machinery, helping to detect imbalances or mechanical faults before they cause damage. This contributes to improved maintenance schedules and reduced downtime.
Seismic Monitoring: Quartz accelerometers are used in geophysical studies, including earthquake monitoring, to measure ground motion. Their precision helps in gathering critical data for early warning systems and scientific research.
Consumer Electronics: Many portable electronic devices, such as smartphones, tablets, and wearables, use quartz accelerometers to detect movement, orientation, and other motion-based activities. These accelerometers are integral to features such as screen rotation, step counting, and fitness tracking.
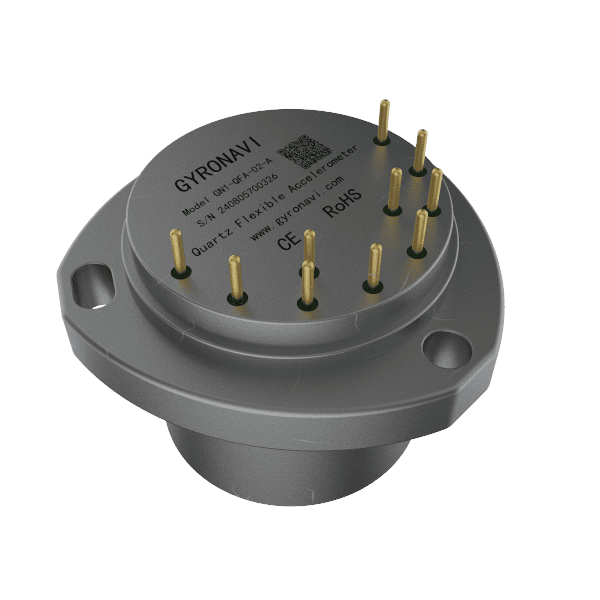
How to Choose the Right Quartz Accelerometer
When selecting a Quartz Accelerometer consider
Precision Requirements: Ensure that the accelerometer meets the level of accuracy required for your application. For high-precision applications like aerospace testing, you may need an accelerometer with very low noise and drift.
Measurement Range: Choose an accelerometer that can measure the acceleration ranges that are relevant to your application. Consider both the lower and upper limits of acceleration that your system will experience.
Temperature Range: Assess the operating temperature range of the accelerometer. If your application involves extreme temperatures (e.g., in aerospace or automotive testing), ensure that the accelerometer can function within the necessary temperature limits.
Physical Size: Consider the available space for the accelerometer in your application. Choose a model that fits within the physical constraints of your system or device.
Power Consumption: For battery-powered applications, consider the power consumption of the accelerometer. Low-power devices will contribute to extended battery life and more efficient operation in remote monitoring systems.
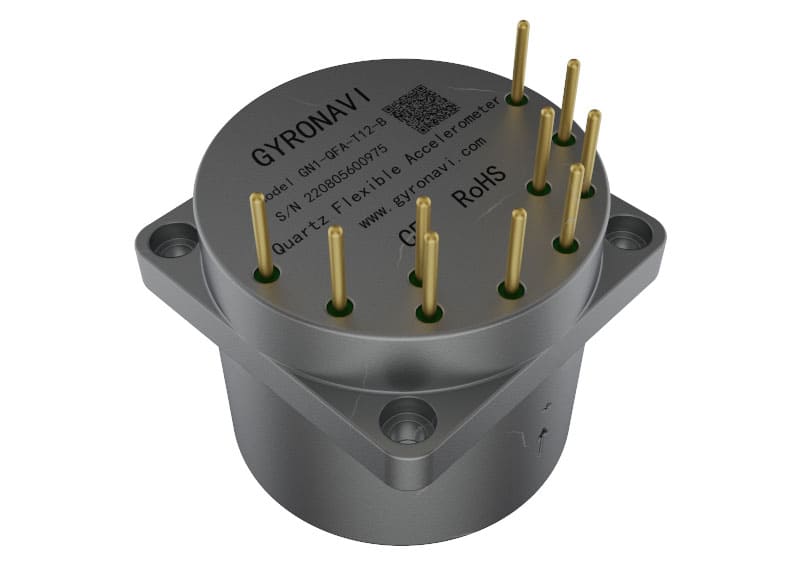
Why Choose Our Quartz Accelerometer?
At GYRONAVI, we understand the importance of precise measurements across various industries. Our quartz accelerometer are not only trusted for their outstanding technical performance, but also for their unparalleled quality assurance and excellent customer service, making them the leading choice in the industry.
Ultra-High Precision and Long-Term Stability
Our quartz accelerometer use industry-leading piezoelectric technology to deliver unmatched precision. Thanks to the high-quality quartz crystals and precision manufacturing processes, our accelerometers provide accurate measurements even in the most complex dynamic environments. Additionally, the long-term stability of the quartz material ensures that our sensors maintain high-precision data over time, minimizing the need for frequent recalibration and reducing maintenance costs.
Exceptional Environmental Adaptability
Our quartz accelerometer have undergone rigorous environmental adaptability testing and are capable of stable operation in extreme temperature, humidity, and vibration conditions. Whether in the freezing cold of the Arctic or the scorching heat of the desert, our accelerometers ensure stable performance. This adaptability makes our products ideal for industries like aerospace, automotive, industrial equipment, and earthquake monitoring. Your equipment and systems can operate seamlessly in harsh environments, ensuring reliable and safe data collection.
Extensive Industry Experience and Market Reputation
As a leading precision sensor manufacturer, GYRONAVI has accumulated extensive experience in the industry, serving sectors such as aerospace, automotive, industrial, military, and earthquake monitoring. We maintain long-term partnerships with several industry-leading companies, earning high praise for our high-quality products and exceptional service. The widespread application and recognition of our products in the market have established us as a trusted partner for our clients.
Strict Quality Control and Certifications
Our production process strictly follows international quality standards, with all quartz accelerometers undergoing rigorous quality testing, including temperature, vibration, and acceleration tests to ensure each product meets design specifications. We are ISO-certified, and all products meet ROHS and CE standards, ensuring compliance with global market quality requirements. These certifications and tests guarantee the reliability and consistency of our products worldwide.
Customization to Meet Specific Needs
We understand that every application has unique requirements, which is why we offer customization services to ensure our quartz accelerometers meet your specific needs. Whether it’s precision, temperature range, or packaging form, we can adjust and optimize our products to perfectly fit your system. By closely collaborating with our clients, we provide tailored solutions for each project to ensure optimal performance.
Reliable After-Sales Support and Technical Service
Choosing GYRONAVI means not only purchasing high-quality products but also benefiting from our comprehensive technical support and after-sales services. Our experienced technical team is available to provide installation assistance, debugging, and consultations during product use. Should you encounter any technical issues, we respond quickly and provide effective solutions.
Our products perform exceptionally well in these fields.
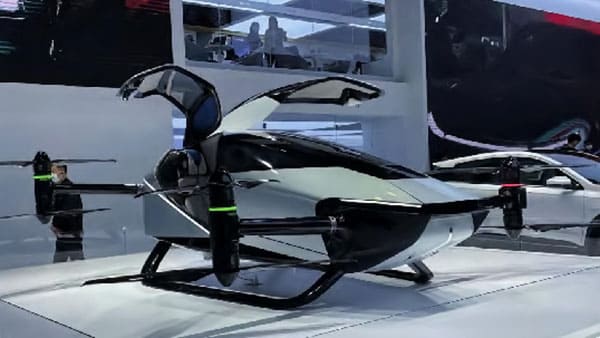
Drone Industry
Our products are widely used in the drone industry, providing precise navigation and stability solutions. Whether for commercial, industrial, or military applications, our advanced sensors and systems enhance the performance and reliability of unmanned aerial vehicles (UAVs).
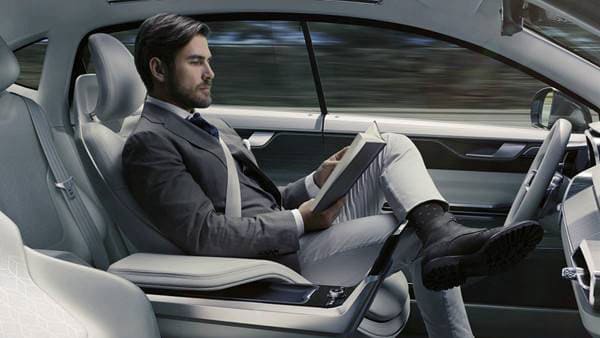
Autonomous Driving Industry
Our products play a crucial role in the autonomous driving industry, providing essential navigation, sensing, and stability solutions. With advanced gyroscopes and inertial measurement units (IMUs), our systems ensure precise control and reliable performance for autonomous vehicles in various environments.
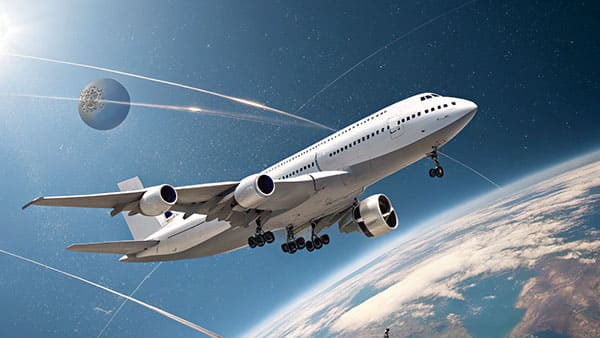
Aerospace Industry
Our products are essential in the aerospace industry, offering high-precision navigation and stability solutions for both spacecraft and satellite systems. With advanced gyroscopes and inertial navigation systems, we provide the reliability needed for critical aerospace applications, ensuring precise performance in even the most demanding conditions.
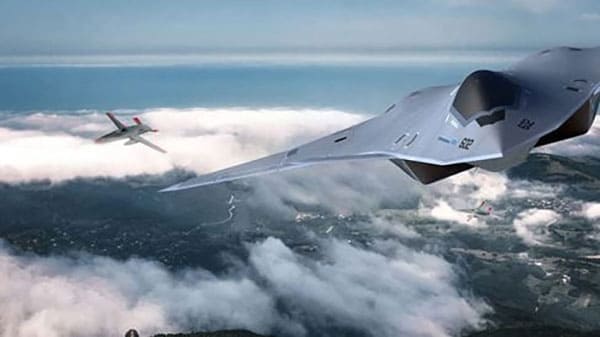
Aviation Industry
Our products are integral to the aviation industry, providing high-precision navigation and stability solutions for aircraft systems. With advanced gyroscopes and inertial measurement units (IMUs), we ensure reliable performance in flight control, navigation, and guidance systems, enhancing safety and operational efficiency.
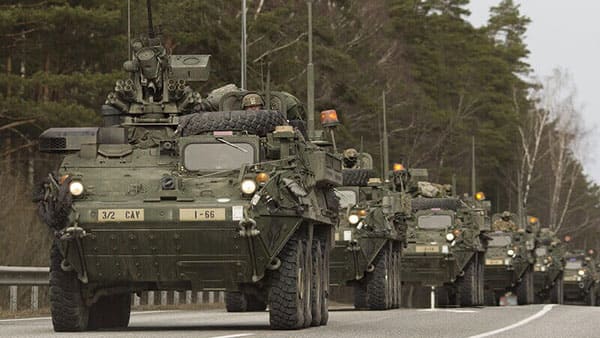
Defense and Military Industry
Our products are critical in the defense and military industry, offering precise navigation, stabilization, and guidance solutions for various military applications. From missile guidance systems to unmanned vehicles, our high-precision gyroscopes and inertial navigation systems ensure reliable performance in demanding and high-risk environments.
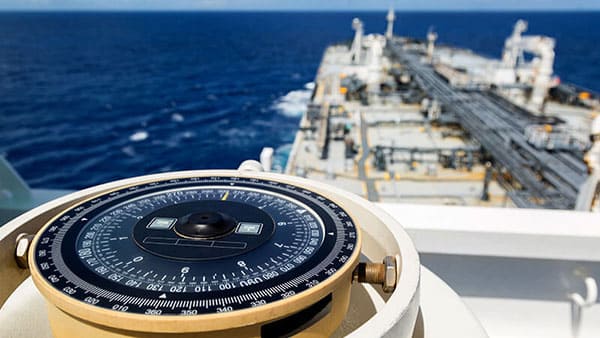
Maritime Navigation and Detection Industry
Our products are vital in the maritime navigation and detection industry, providing precise and reliable solutions for underwater and surface vessels. With advanced gyroscopes and inertial navigation systems, we support accurate positioning, navigation, and detection, ensuring safe and efficient operations in challenging marine environments.
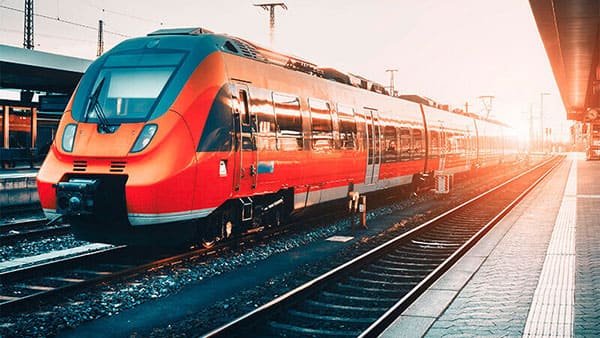
Rail Transit Industry
Our products are essential in the rail transit industry, providing reliable navigation and stability solutions for trains and other rail vehicles. With high-precision gyroscopes and inertial navigation systems, we ensure safe, efficient, and accurate operation of rail systems, supporting both on-board control and infrastructure management.
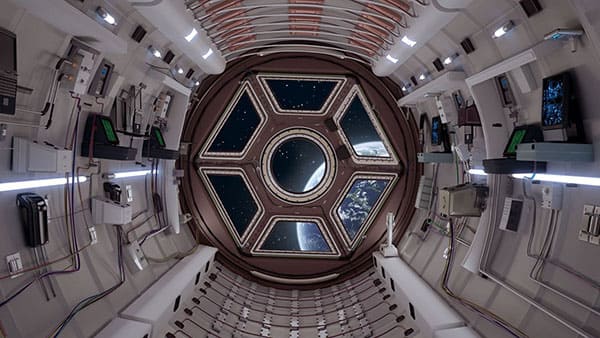
Space Exploration Industry
Our products are crucial in the space exploration industry, offering precise navigation and orientation solutions for spacecraft, rovers, and satellites. With advanced gyroscopes and inertial measurement units (IMUs), we ensure reliable performance in the extreme conditions of space, supporting accurate positioning and stability during missions to explore the universe.
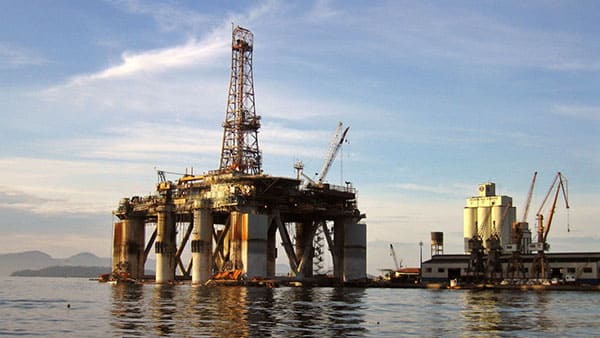
Geological Exploration Industry
Our products play a key role in the geological exploration industry, providing accurate and reliable navigation and measurement solutions for surveying equipment, drilling systems, and exploration vehicles. With high-precision gyroscopes and inertial navigation systems, we ensure precise positioning and stability, even in challenging and remote environments.
After-Sales Service
At GYRONAVI, we understand that reliability and precision are crucial in the field of inertial navigation systems. That’s why we not only provide cutting-edge products but also offer a robust after-sales support structure designed to keep your systems running smoothly, ensuring uninterrupted business operations. With our 7 days, 12 hours service and 3-year warranty, you are not just buying products — you’re securing a long-term partnership for continuous support and success.
Why Choose Our After-Sales Service?
- 12-Hour Technical Issue Resolution: We guarantee to resolve your product’s technical issues within 12 hours.
- 3-Year Warranty: All products come with a comprehensive 3-year warranty for peace of mind.
- Expert Technical Support: Our team is ready to assist with any technical queries or issues regarding our products.
- Global Service Network: We provide tailored support with fast response times, no matter where you’re located.
- Spare Parts Availability: A well-stocked inventory ensures quick replacement of parts to minimize downtime.
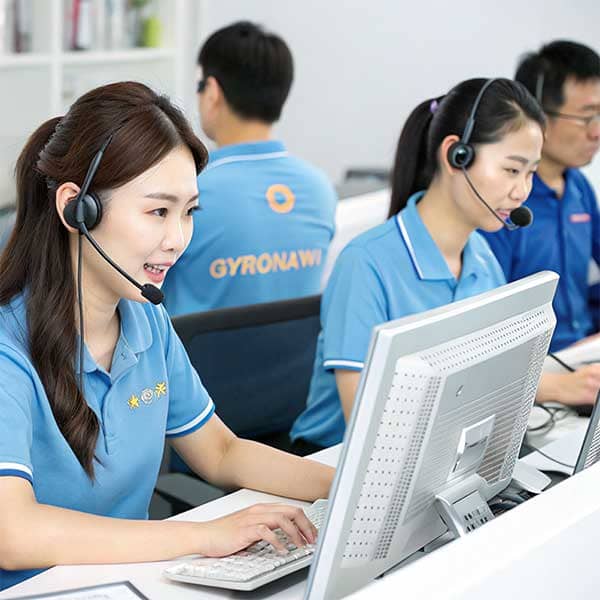
FAQs
Can quartz accelerometers work in extreme environments?
Yes, quartz accelerometers are highly adaptable to extreme conditions. They can function effectively in a wide temperature range, resist mechanical shock and vibration, and provide stable measurements in both high and low temperature environments, making them ideal for applications in harsh conditions.
What is the lifespan of a quartz accelerometer?
The lifespan of a quartz accelerometer can range from 10 to 20 years, depending on usage and environmental factors. Their durability and long-term stability make them a reliable choice for long-term applications without significant degradation of performance.
What is the difference between quartz accelerometers and other types of accelerometers?
Quartz accelerometers use the piezoelectric properties of quartz crystals, while other accelerometers may use capacitive, resistive, or MEMS-based technologies. Quartz accelerometers are known for their high stability, precision, and resistance to environmental factors, making them ideal for high-accuracy applications.
Can quartz gyroscopes operate in extreme temperature conditions?
Yes, quartz gyroscopes are available in models that can operate in extreme temperature conditions, such as in high-temperature industrial or aerospace applications.
Can quartz accelerometers measure both static and dynamic acceleration?
Yes, quartz accelerometers can measure both static and dynamic accelerations. They are suitable for applications that require monitoring of constant acceleration (static) as well as fluctuating or rapidly changing accelerations (dynamic).
How is the output of a quartz accelerometer presented?
The output of a quartz accelerometer is typically presented as an electrical signal, which can be in the form of voltage, current, or frequency, depending on the specific design. This signal corresponds to the magnitude of the measured acceleration and is processed by associated electronics for further analysis.
What is the response time of a quartz accelerometer?
The response time of a quartz accelerometer depends on the specific model, but it is generally very fast, with many models capable of providing real-time acceleration data with response times in the range of milliseconds or microseconds.
Are quartz accelerometers affected by magnetic fields?
Quartz accelerometers are generally not affected by magnetic fields, unlike some other types of accelerometers, such as MEMS-based sensors. This resistance to magnetic interference makes them ideal for use in environments where electromagnetic fields are present.
Can quartz accelerometers be used in underwater applications?
Yes, quartz accelerometers are suitable for underwater applications. Their high reliability and resistance to environmental factors such as humidity and corrosion make them ideal for use in underwater and marine environments, where high-pressure conditions are common.
Can quartz accelerometers measure both linear and rotational accelerations?
Quartz accelerometers are primarily designed to measure linear accelerations, but when paired with other sensors like gyroscopes, they can be used to measure rotational accelerations as part of an inertial measurement unit (IMU).
Get Your Customized Motion Control Solutions Today
Choosing GYRONAVI’s quartz accelerometer means selecting high precision, high stability, environmental adaptability, and cost-effectiveness. No matter how harsh your operating environment or how unique your requirements, we can offer tailored solutions that ensure the most accurate and reliable measurements. Additionally, we are committed to providing world-class technical support and after-sales service, ensuring the long-term stable operation of your products.By choosing GYRONAVI, you are not just selecting a supplier, but a comprehensive partner committed to providing continuous support and efficient solutions for your projects. Contact us now to experience our custom-designed, high-performance accelerometer products and take your business to greater success!